Solving Lab Safety Challenges, Both New and Old
Dan J. Scungio, MLS (ASCP), SLS, CQA (ASQ), discusses recent developments in lab safety and how to address key challenges.
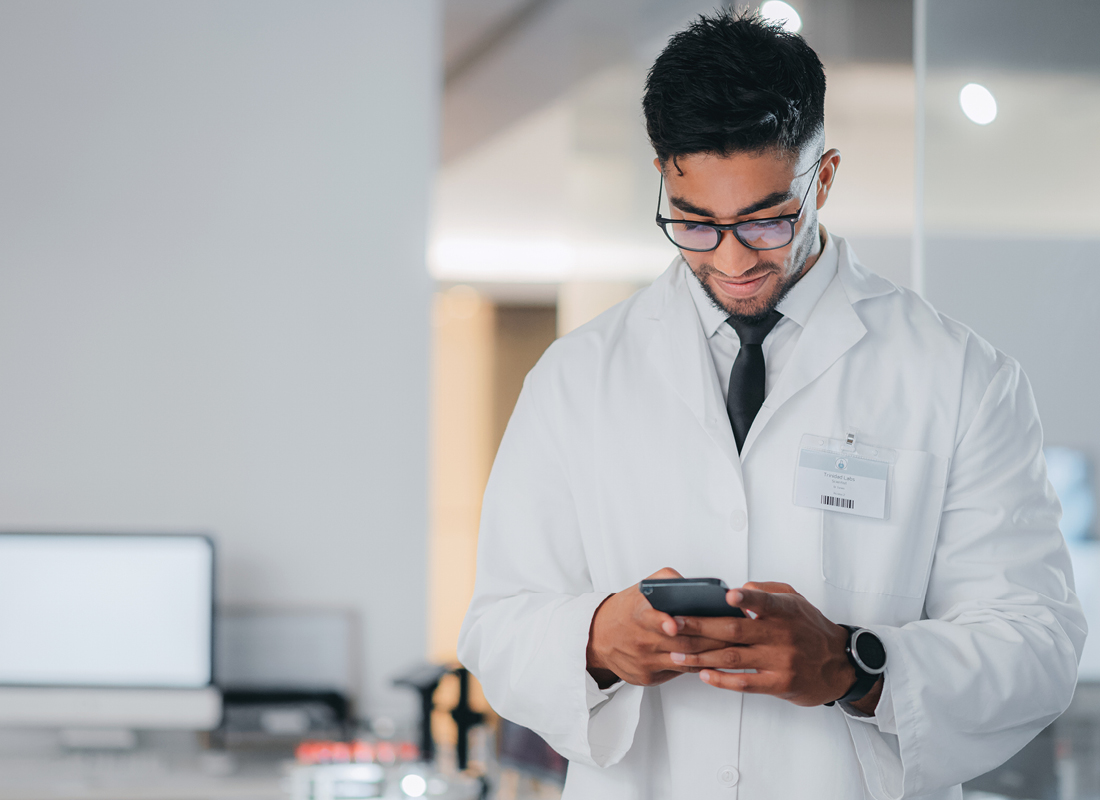
Key lab safety challenges, such as personal protective equipment (PPE) noncompliance, have been the same for decades. However, newer challenges such as personal device usage in the laboratory have emerged. Lab safety expert Dan J. Scungio, MLS (ASCP), SLS, CQA (ASQ), discusses recent developments in lab safety, as well as how lab professionals can handle challenges—both new and old—in their facilities.
Q: What have been the major developments in clinical lab safety over the last few years?
A: It was the COVID-19 pandemic, which did not have a technology impact or regulatory impact; it had more of an event impact. It was definitely a learning experience for lab safety professionals. One of the things we learned was, you better have staffing management in your emergency management plan. This is where it really hit home and got lab leaders thinking about questions such as, “How are we going to operate a laboratory without enough staff? What are our backup plans? What are our alternatives? Can we go to point-of-care testing, do we have a sister hospital we can send things to, and can they handle the volume?” Answers to those questions should now be part of everybody’s lab emergency management plan.
Another development in clinical safety involves technology changes. Cellphones and smartwatches aren’t new, but they’re a newer problem in a lab setting because of the infection control risk. Is new technology, such as AI, going to continue to bring new challenges with safety in the labs? It depends on what’s brought into the lab. We’ll have to deal with those things as they evolve.
Q: What are the most common lab safety challenges your clients come to you with?
A: The most common questions I receive can be categorized into three different areas: 1) Chemical management, which is a huge topic with a lot of regulations; 2) Compliance with PPE, which should be a basic, but there are lots of labs where it’s a problem, whether that’s due to human behavior or leadership not enforcing it as well as they could; and 3) personal electronic devices—cellphones, earbuds, all those things that shouldn’t be in a laboratory because of infection control reasons.
Q: What are some solutions to these challenges?
Chemical Management: It depends on what specific questions people have. Sometimes it’s storage, sometimes it’s inventory management, sometimes it’s just general chemical safety best practices. Labs have asked me to come in and look at their chemical management specifically asking, “Is our storage correct? Are we prepared for spills?” Sometimes they’ll ask me to take a look with an outside pair of eyes in their labs, and then look at their specific issues.
PPE: You definitely have to get manager involvement when it comes to PPE. And you also have to have management modeling. So, if your manager comes in and does a huddle in the lab every shift for 10 minutes and doesn’t wear any PPE, they’re not modeling very well. They’re not meaning to, but they’re telling their lab staff that this is not important to them. What managers do is watched closely, and it’s important that they’re following the guidelines as well.
Personal devices: If humans have a basic need for something, they’re going to work around to get that need met. That includes addictions to things like cellphones or social media. A friend of mine, who also works in lab safety, said that maybe the answer is a 10-minute e-break every hour, so that people can have those needs met. Having your cellphone, smartwatch, or other devices in the laboratory has led to infections and hospitalizations of laboratory personnel, so it’s dangerous. But it’s a hard one to overcome because such technology is so pervasive.
Q: How can clinical lab leaders ensure that safety is maintained in their labs during challenging times?
A: If a laboratory is facing economic challenges, obviously, they’re not cutting back on PPE purchases, with engineering controls, or things like that. Those are things that have to be in place regulatorily. But when you’re going through economic situations, that’s very hard in a lab and on the leaders. The last thing on their mind, probably, is safety. That difficult time doesn’t always mean cutbacks, however, it could also mean growth. I’ve done consulting for some of those labs that expanded rapidly during the pandemic because they were not able to keep a handle on their safety program as they were going through their rapid growth.
If you’re growing fast, or cutting back, you still have to keep your eye on your safety program overall. And that means looking at your number of spills and exposures, incidents and accidents, and keeping up with your chemical inventory. You have to make sure that you’re doing annual audits, monthly physical environment audits, and whatever else is required no matter what situation you’re in. If you’re in a cutback situation and the staff that have been in charge of some of those safety responsibilities have been let go, you need to figure out who’s going to do those now. Those duties don’t go away, they’re still required. You can’t really skimp on safety. Otherwise, the few people you have left are going to be injured, exposed, and out of work. And you can’t afford to have that happen.
Q: What are the biggest challenges that lab staff have in complying with OSHA or other regulations?
A: When somebody’s doing something that’s unsafe, the first thing you have to remember is there are probably several sources of influence on their behavior. Why are they doing that? There are probably several reasons, but your first thoughts might be, “Oh, they’re just being lazy, or they’re doing it because they don’t want to, and they’re just being resistant.” We tend to think that people are doing things for, ‘evil’ reasons when they don’t comply. And usually that’s not the case. Usually there’s an education component that might be missing. And I’m not just talking about onboarding because you can onboard somebody with safety, but it has to continue. You have to have ongoing safety education and review of safe work practices in your labs. Because doing it once is not going to maintain that good safety practice. So, does it mean they didn’t get education, or didn’t they get a complete education? Maybe they implemented some new practices and nobody told the lab safety department that there’s a new process that needs a risk assessment.
Recommended resources for staying on top of lab safety developments:
• Lab safety-related magazines and periodicals
• OSHA website and emails/e-newsletters
• CDC emails/e-newsletters
• Dan’s “Dan the Lab Safety Man” lab safety e-newsletter
• Emails from laboratory organizations (American Society for Clinical Pathology, American Society for Clinical Laboratory Science, Association for Diagnostics & Laboratory Medicine, College of American Pathologists, etc.)
Q: What can lab leaders do in situations like these?
A: The first thing to do when you see noncompliance is ask the staff member questions and figure out why it’s happening. It could be as simple as somebody just heard upsetting news. Or it could be something else. I was talking to a fairly new staff member about not wearing a lab coat, but the lab coats were in a storeroom that had a number lock on it, and they didn’t know the combination. They were kind of shy and didn’t want to ask. Once we got to the bottom of it, we solved the problem. If you don’t make it easy for people to do the right thing, they’re less likely to do it. So, if you want them to take off their lab coat before going into the break room, have some hooks hanging outside the break room so they have a place to put lab coats. Make it easy for staff to do the right thing. My favorite line for enforcing lab coat use is, “What size can I get you?” This automatically lets them know that it’s mandated here, you’ve got to have it. It’s just a simple question. It speaks volumes about what the requirements are and your culture.
Q: What advice do you have for anyone who’s new to the lab safety role?
A: Don’t hesitate to ask questions or reach out to resources. I remember being new about 15 years ago in lab safety, and it’s a scary place out there. You need a lot of help. I always tell people, “Please, feel free to email me questions.” I answer them all the time. I always say, “Give yourself time to become an expert.” Look at some opportunities for certification like the American Society for Clinical Pathology’s Qualification in Lab Safety (QLS). There are resource books that people can use to study for the exam, but also that can help you learn about lab safety.
________________________________________________________________________________________________________________________________________
Dan J. Scungio, MLS (ASCP), SLS, CQA (ASQ), has over 30 years of experience as a certified medical technologist. He has a bachelor’s degree in medical technology from the State University of New York at Buffalo in Amherst and Buffalo, New York. Dan worked as a laboratory generalist in hospitals ranging in size from 75 to 800 beds before becoming a laboratory manager. After 10 years of lab management, he became the laboratory safety officer for a system of 12 hospitals and over 20 laboratories and draw sites in Virginia and North Carolina.
Subscribe to view Essential
Start a Free Trial for immediate access to this article