Special Report: The OSHA Inspection Process and How to Survive It
The basics of how the OSHA inspection process works and how laboratories can successfully navigate it.
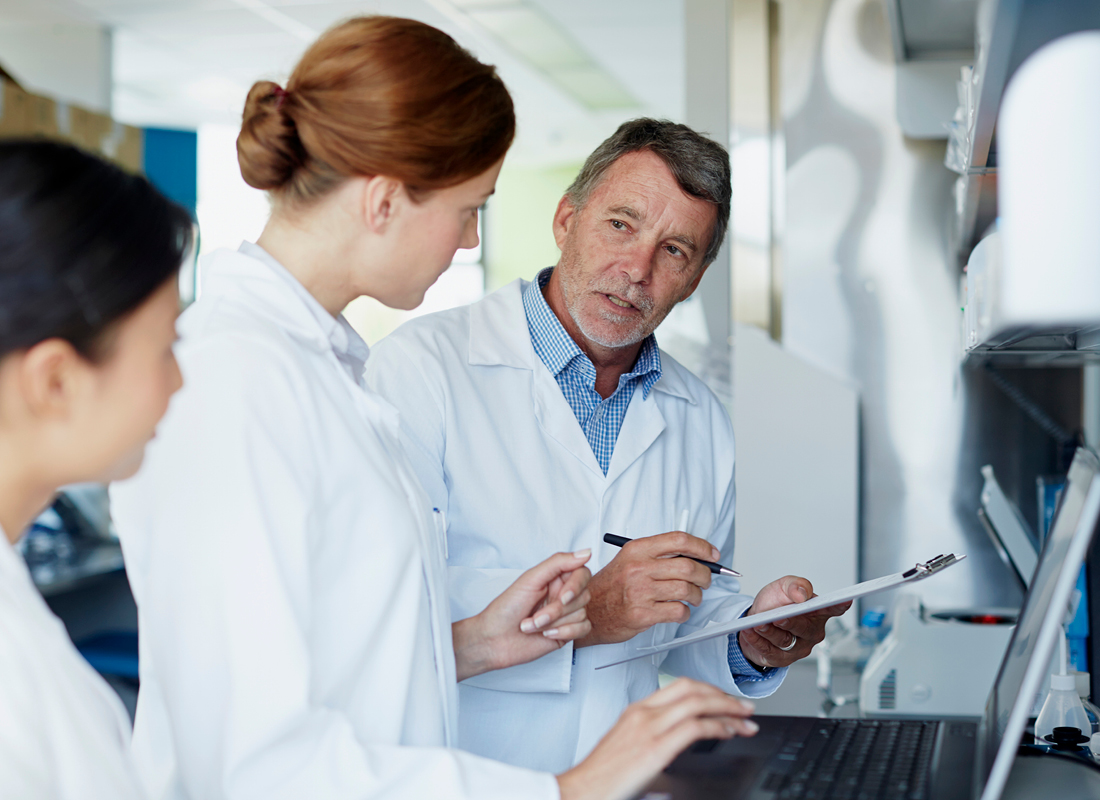
An Occupational Safety and Health Administration (OSHA) inspection can be an intimidating experience, but it doesn’t have to be. Knowing how the OSHA inspection process works can help you minimize the disruptive effect of inspections, reduce the risk of citations, and—if necessary—reduce potential fines and penalties.
The positives of an OSHA inspection
It’s important to remember that OSHA inspections are meant to identify and correct safety issues, and are mainly a positive thing, according to laboratory professionals.
G2 Intelligence recently did a mini survey of lab safety representatives regarding OSHA inspections, who pointed out that such inspections should not be feared. In their suggestions for how to survive an OSHA inspection, respondents said it’s important to remind staff that OSHA is not the enemy, and inspectors are there to help. “Create a working environment where a pending inspection is welcomed,” one survey respondent recommended.
Another respondent pointed out that the findings of such inspections can help lab leaders show a lack of resources to upper management. “As a non-revenue generating department, it is difficult to convey to upper management/administration that safety tasks are important when success is very difficult to measure,” the respondent wrote. Other tips shared by survey respondents included:
-
- Pro-actively work on reducing the incident rate
-
- Conduct internal inspections
-
- Have all documentation in order
- Demonstrate that effort is being made when it comes to safety
OSHA Penalties, 2023
OSHA adjusts penalties each year for inflation. Here are the 2023 amounts, which OSHA will adjust in December:1
OSHA Civil Penalties, 2023
Type of Violation | Minimum Penalty | Maximum Penalty |
Other-Than-Serious | $0 per violation | $15,625 per violation |
Serious | $1,116 per violation | $15,625 per violation |
Willful or Repeated | $11,162 per violation* | $156,259 per violation |
Posting Requirements | $0 per violation | $15,625 per violation |
Failure to Abate | N/A | $15,625 per day unabated (up to 30 days) |
Source: OSHA, “2023 Annual Adjustments to OSHA Civil Penalties, December 20, 2022 Memorandum.”1
OSHA also imposes Gravity Based Penalties (GBPs). In 2023, GBPs were:1
-
- $15,625 for a high gravity violation
-
- $8,929 to $13,394 for a moderate gravity violation
- $6,696 for a low gravity violation.
How OSHA decides who to inspect
Federal OSHA has only about 1,850 inspectors responsible for 130 million workers. That’s a ratio of one inspector for every 70,000 workers.2 The agency carried out 31,820 inspections in 2022.3 Those statistics don’t include inspections conducted by the 27 states with their own OSHA State Program.4
Thus, statistically at least, the odds that your lab will undergo an OSHA inspection are long. But all businesses aren’t at equal risk of an inspection. The OSHA Field Operations Manual establishes priorities for deciding who to inspect:5
-
- First Priority: Inspections responding to reports of imminent danger.
-
- Second Priority: Inspections after fatalities or accidents serious enough to send at least three workers to the hospital.
-
- Third Priority: Inspections in response to employee complaints or referrals from other government agencies.
- Fourth Priority: Programmed inspections, including under the Site-Specific Targeting Program which focuses on employers that report high illness and injury rates, and special emphasis programs focusing on particularly hazardous work.
OSHA also does follow-up inspections of employers previously inspected.
Scope of an OSHA inspection
The scope of an OSHA inspection depends on the situation, facility, and reason for inspection. OSHA conducts two kinds of inspections:6
-
- Comprehensive inspections look at all or substantially all potentially hazardous conditions, operations, and practices within a workplace.
- Partial inspections are limited to certain potentially hazardous areas, operations, conditions, or practices in the workplace.
OSHA inspectors have discretion to convert a partial to a comprehensive inspection if they find indications of problems during the early phases of the inspection.
When the OSHA inspector first arrives
OSHA usually conducts inspections during the workplace’s regular working hours. In most cases, OSHA inspectors show up unannounced. When the inspection begins, the OSHA inspector must present credentials to the owner, owner representative, operator, or agent in charge.
Best Practice: Politely ask to see the credentials of the OSHA inspector if they’re not presented to you.
You can’t refuse to let an OSHA inspector enter your facility. But you may ask the inspector to get a warrant to conduct the inspection before entering and refuse entry without one. Exceptions: You can’t refuse entry for lack of a warrant if you or one of your representatives has already given consent to the inspection or if there’s an emergency or urgent reason for the inspector to enter.
Best Practice: Keep in mind that while asking for a warrant may be within your rights, it also makes the inspector’s job more difficult, which may, consciously or unconsciously, affect the way they carry out the inspection once the warrant is secured. So, don’t insist on a warrant simply to stall for time but only when legal counsel advises you to do so.
Once inspectors get the warrant, you must let them in and refrain from interfering with their inspection. However, you may require OSHA inspectors to follow the same policies, procedures, and rules as any other employee or visitor, such as wearing mandatory personal protective equipment (PPE).
Best Practice: Train staff on the OSHA inspection process and what to do if an inspector shows up. Appoint a contact person and instruct them to notify other necessary lab officials, escort the inspector directly to a pre-determined area (conference room or office), and remain with the inspector until a lab official arrives. Tell the contact person to only take the inspector through the designated area of your facility until you determine the purpose of the inspection.
Have representative accompany OSHA inspector
OSHA inspectors will ask if you want a representative to participate in the inspection. According to the regulations, one or more employer and/or employee representatives may accompany the inspector “during the physical inspection of any workplace for the purpose of aiding such inspection.”7
Best Practice: Training a representative in advance on how to monitor an OSHA inspector is a good way to protect yourself. For example, there have been situations in which violations were dismissed because the employee representative noticed that the inspector did something improper. Consider using the person you designate as the contact person as your representative.
Opening conference
The inspector must notify “all affected employers” of the inspection’s purpose and furnish a copy of the complaint, if there is one. Before conducting the inspection, the inspector is supposed to hold a brief meeting with employers and employees called the opening conference. During the conference, inspectors will explain why they’re there and what to expect during the inspection.6
Best Practice: The opening conference is critical because you have a right to know the purpose and reason for the inspection. If you don’t understand the purpose or reason, politely ask the inspector for an explanation. Demonstrate your willingness to cooperate.
Best Practice: Don’t hide anything, but also don’t offer information that’s not requested and not relevant to the purpose of the inspection during the opening conference.
There are two kinds of opening conference. In a joint conference, the investigator meets with both the employer and the employees or employee representative at the same time. Inspectors are supposed to encourage joint conferences in the interest of open communication. But if the employer or employees object, the inspector will conduct separate conferences with each group.
The walkaround inspection
The most crucial phase of the inspection is the walkaround during which the inspector walks around your facility looking for potential safety and health hazards and evaluates whether the facility meets OSHA standards. During the walkaround, inspectors may exercise broad powers to gather information relating to your lab’s compliance:6
Take photographs: Inspectors may take photographs and/or video if they consider it necessary. For example, the inspector may want to take a picture of a testing machine that lacks a proper guard to document a violation. You have a right to get a copy of any photographs, videos, or voice recordings taken during the inspection. OSHA must also keep any trade secrets or other sensitive business information contained in such photographs, videos, and voice recordings confidential.
In a comprehensive inspection, inspectors can look at almost anything. In a limited inspection, inspectors may photograph or video record only things that relate to the subject of the investigation. So, for example, it would be inappropriate for inspectors to photograph equipment in the titration room if they’re investigating a complaint about ergonomically unsafe keyboards in the office. Inspectors may also widen the scope of an investigation if they notice an imminent danger during the walkaround.
Collect samples: OSHA inspectors may collect samples, including air and/or surface sampling. You have the right to get summaries of the results—but only if you request them.
Conduct interviews: Inspectors may interview employees to ask them to point out hazardous conditions and other matters relevant to the inspection. Inspectors can interview employees in private if they deem it necessary. Employee statements are confidential but can be used in court hearings. Although generally held during the walkaround, employee interviews may be held at any time during the inspection.
Record reviews: Inspectors may review records like OSHA 300 logs and accident reports before, during, or after the walkaround.
Let you fix problems on the spot. Inspectors may offer suggestions or help in correcting deficiencies or hazards noted during the walkaround and even give you an opportunity to fix the problem before the end of the inspection to avoid a citation.
Best Practice: Have your representative carry a digital or video camera with them on the walkaround and take pictures of the items the inspector points out. If an inspector takes a picture or video records something, the representative should, too. This way you’ll have an accurate pictorial record in case the inspector’s report of the problem conflicts with your own.
Best Practice: Instruct the representative to write down everything the inspector says, and even consider taking a video or voice recorder along during the inspection so you can record the inspector’s every word. Don’t be afraid to ask questions.
Best Practice: Instruct the representative to be as helpful and informative as possible and not to argue with or hurry the inspector. Though it may seem like common sense, it’s also important to remind the representative to refrain from making condescending remarks, derogatory comments, political opinions, jokes, or any other communications that may be viewed as offensive.
Best Practice: OSHA inspectors cannot accept anything from the employer such as a gift or even lunch. So don’t offer them anything but cooperation.
Best Practice: While representatives should remain friendly and upbeat, they shouldn’t try to be best friends with the inspector.
Closing conference
After the actual inspecting is over, the inspector will hold a closing conference to describe the results of the inspection, including any violations found and how long you have to correct them. Like the opening conference, the closing conference is attended by the employer and employee representatives, either jointly or separately, depending on the circumstances.6
Best Practice: If you paid attention during the walkaround, you’ll probably know what violations or concerns the inspector will bring up during the closing conference. Be prepared to provide explanations and estimates of when you can abate those violations at the closing conference.
Inspectors may hold a second closing conference in person or by phone if they didn’t have all the necessary information at the first conference.
Citation and abatement
If you get cited for an OSHA violation, you’ll receive copies of the citations by certified mail. The citation will list an abatement date, that is, a deadline for correcting the problem. You can contest the abatement date if you think you need more time, but you must do so in writing and file your response within 15 working days after getting the copy of the citation.8
You must post copies of any citations you receive in a part of your workplace that’s accessible to all employees and leave them posted for at least three days or until you abate the violation.9
Once you fix the problem, you must provide evidence of abatement and be able to document your compliance.
Follow-up inspection
OSHA may do a follow-up instruction to ensure you corrected any violations you were cited for. If fixing the problem is likely to take a long time, OSHA may also perform a monitoring inspection to ensure that hazards are being corrected and employees are being protected while the abatement proceeds. OSHA won’t normally do a follow up or monitoring inspection if you provide evidence that you’re abating the problem. Such inspections are generally used when an employer has been cited for willful or repeat violations. Follow-up or monitoring inspections are also more likely to be used when the citation is due to the employer failing to abate a violation and/or the violation creates an imminent danger.6
References:
Subscribe to view Premium
Start a Free Trial for immediate access to this article